The Controller Area Network, or CAN bus, is a robust vehicle bus standard designed to allow microcontrollers and devices to communicate with each other’s applications without a host computer. It is a message-based protocol, designed originally for multiplex electrical wiring within automobiles to save on copper, but is also used in many other contexts. In this article, we will delve deep into the world of CAN bus, exploring its origins, its technical specifications, and its applications in various industries. By the end of this comprehensive guide, readers will have a solid understanding of the CAN bus system, its significance in the automotive and industrial sectors, and its potential for future applications.
Automotive CAN Bus Basics, the Controller Area Network
Table of Contents
- History and Development
- Technical Specifications
- Other Applications of CAN bus
- Advantages and Limitations
- Frequently Asked Questions
- Final Thoughts
- Sources
History and Development
The CAN bus, or Controller Area Network, is a testament to the evolution of technology in the automotive and industrial sectors. Its development was driven by the need for a more efficient and streamlined method of communication between various electronic components in vehicles. This section will delve into the history and development of the CAN bus, tracing its origins, its adoption, and its evolution over the years.
Origins of the CAN bus
The inception of the CAN bus is deeply rooted in the technological advancements of the late 20th century. As vehicles began to incorporate more electronic components, the need for a more efficient communication system became evident. The traditional point-to-point wiring systems, which had been the norm for years, were becoming increasingly untenable due to several reasons:
Complexity
Each new electronic component added to a vehicle required its own set of wires to connect to every other component it needed to communicate with. This led to a complex web of wires crisscrossing throughout the vehicle. As more and more electronic features were added to vehicles, from advanced entertainment systems to safety and diagnostic tools, the wiring complexity grew exponentially.
Weight and Cost
The sheer amount of copper wiring required in traditional systems added significant weight to vehicles. This not only affected the vehicle’s fuel efficiency but also its overall performance. Additionally, the cost of copper, coupled with the labor-intensive process of installing intricate wiring systems, drove up manufacturing expenses.
Reliability Issues
With an intricate web of wires, the chances of a malfunction or a short circuit increased. Diagnosing and fixing these issues became a time-consuming and expensive endeavor. Moreover, the more complex the system, the higher the chances of potential failures, leading to safety and reliability concerns.
Given these challenges, the automotive industry was in dire need of a solution that could streamline electronic communications within a vehicle. The vision was clear: a system where multiple electronic devices could communicate with each other without the need for direct, individual connections.
Enter Bosch. Recognizing the industry’s needs and the potential for innovation, the company embarked on a mission in the early 1980s to develop a new communication protocol. This protocol would allow for multiple electronic components to communicate over a single data bus, drastically reducing the amount of wiring required and addressing the aforementioned challenges.
The result of this endeavor was the Controller Area Network or CAN bus. Introduced by Bosch in 1986, the CAN bus was a revolutionary step forward in vehicular electronic communications, setting the stage for a new era of interconnected systems and paving the way for the vehicles of the future.
Bosch’s Role in Development
Bosch, a name synonymous with innovation in the automotive sector, played a pivotal role in the development of the CAN bus. The company’s foresight and commitment to addressing the challenges faced by the automotive industry led to the creation of a communication system that would revolutionize vehicular electronics.
The Initial Spark
The journey began in the early 1980s when Bosch identified the growing challenges associated with the traditional point-to-point wiring systems in vehicles. The company realized that as vehicles incorporated more electronic features, the existing wiring systems would become increasingly untenable. Bosch envisioned a more streamlined, efficient, and reliable method of communication between electronic components.
Research and Development
Under the leadership of engineer Robert Bosch, a dedicated team was assembled to tackle this challenge. The team’s objective was clear: develop a communication protocol that would allow multiple electronic devices to communicate over a single data bus. This would not only reduce the complexity of wiring but also enhance the reliability and efficiency of electronic communications within vehicles.
The R&D team at Bosch worked diligently, experimenting with various protocols and communication methods. They sought a solution that would be robust enough to handle the noisy environment of a vehicle, flexible enough to accommodate various devices, and efficient enough to ensure timely communication between components.
Introduction of the CAN Protocol
After years of research and development, in 1986, Bosch introduced the first version of the CAN protocol. This was a message-based protocol, designed to allow microcontrollers and devices within a vehicle to communicate without the need for a central computer. The protocol was designed to be fault-tolerant and could operate in a high electromagnetic interference environment, making it ideal for automotive applications.
The CAN protocol’s introduction was a game-changer. It offered a solution to the myriad of challenges faced by the automotive industry, providing a more streamlined, reliable, and efficient method of communication between electronic components.
Collaboration and Standardization
Recognizing the broader potential of the CAN protocol beyond just automotive applications, Bosch took steps to collaborate with other industry stakeholders and standardization bodies. Their efforts culminated in the CAN protocol being standardized under the ISO 11898 series in 1993, further bolstering its adoption across various industries.
Bosch’s role in the development of the CAN bus cannot be overstated. Their vision, dedication, and commitment to innovation led to the creation of a communication system that has become the backbone of electronic communications in vehicles and various other industries. The CAN bus stands as a testament to Bosch’s legacy of pioneering solutions that address real-world challenges.
Adoption in the Automotive Industry
The introduction of the CAN bus by Bosch in the mid-1980s marked a significant turning point in automotive electronics. However, the journey from its inception to widespread adoption in the automotive industry was both fascinating and indicative of the industry’s evolving needs and priorities.
Early Adopters
Mercedes-Benz was among the first to recognize the potential of the CAN bus. In 1992, they integrated the CAN bus into their flagship W140 S-Class model. This move was groundbreaking. By adopting the CAN bus, Mercedes-Benz showcased a commitment to innovation, setting a precedent for other manufacturers. The success of the CAN bus in the W140 S-Class, particularly in streamlining communication between complex systems like engine management, ABS, and airbags, made a compelling case for its broader adoption.
The Ripple Effect
Following Mercedes-Benz’s lead, other automotive giants began to take notice. The early 1990s saw companies like BMW, Audi, and Ford integrating the CAN bus into their vehicles. The benefits were clear: reduced wiring complexity, weight savings, increased reliability, and the ability to add new features without overhauling the entire system.
Standardization and Expansion
The CAN bus’s growing popularity in the automotive sector caught the attention of standardization bodies. In 1993, the International Organization for Standardization (ISO) standardized the CAN bus under the ISO 11898 series. This standardization further facilitated its adoption, ensuring consistency and compatibility across different manufacturers and models.
By the late 1990s and early 2000s, the CAN bus had become an industry standard. Almost every major car manufacturer globally had integrated the CAN bus into their vehicles, from luxury models to everyday commuter cars.
Evolution with Technology
As technology advanced, so did the applications of the CAN bus in vehicles. Beyond just basic communication between electronic components, the CAN bus began to play a crucial role in advanced driver assistance systems (ADAS), infotainment systems, and even in electric and hybrid vehicle management.
Manufacturers started to implement multiple CAN networks within a single vehicle, each dedicated to specific functions – a high-speed CAN for powertrain systems, a lower-speed CAN for body-related functions, and so on.
Challenges and Innovations
While the adoption of the CAN bus brought numerous advantages, it wasn’t without challenges. As vehicles incorporated more electronic systems, the data traffic on the CAN bus increased, leading to potential bottlenecks. The industry responded with innovations like CAN FD (Flexible Data-Rate), introduced by Bosch in 2012, which allowed for faster data transmission rates.
The adoption of the CAN bus in the automotive industry is a story of innovation, collaboration, and evolution. From its early days as a solution to wiring complexity to its modern role as the backbone of automotive electronics, the CAN bus has proven to be an indispensable tool in shaping the cars of today and tomorrow.
ISO Standardization
The International Organization for Standardization (ISO) plays a crucial role in ensuring that technologies and systems across industries adhere to consistent standards, facilitating interoperability, safety, and reliability. The CAN bus, given its transformative impact on the automotive and industrial sectors, naturally drew the attention of ISO. The process of standardizing the CAN bus under ISO not only bolstered its credibility but also paved the way for its broader adoption across various industries.
The Need for Standardization
As the CAN bus began to gain traction in the automotive industry, the need for a standardized protocol became evident. Different manufacturers adopting their own variations of the CAN protocol could lead to compatibility issues, hindering the technology’s potential. A standardized approach would ensure that devices and systems from different manufacturers could seamlessly communicate with each other, fostering innovation and ensuring safety.
ISO 11898 Series
In 1993, the ISO introduced the ISO 11898 series, which specifically addressed the CAN bus. This series defined the standard for high-speed (up to 1 Mbit/s) and fault-tolerant medium-speed (up to 125 Kbit/s) communication within vehicular networks. The standard covered various aspects of the CAN bus, including:
- Physical Layer: Defined the electrical characteristics of the bus, including voltage levels, signaling, and termination.
- Data Link Layer: Addressed the framing, arbitration, error detection, and signaling.
- Application Layer: While the ISO 11898 series primarily focused on the lower layers, it provided a foundation upon which other standards (like ISO 15765 for diagnostics) could define application-specific communication over CAN.
Implications of Standardization
The standardization of the CAN bus had several significant implications:
- Interoperability: Manufacturers could now develop systems and components with the confidence that they would be compatible with other CAN-based systems, irrespective of the manufacturer.
- Innovation: With a standardized foundation, companies could focus on building innovative applications and solutions on top of the CAN protocol without worrying about the underlying communication intricacies.
- Broader Adoption: The ISO stamp of approval gave industries outside of automotive – like industrial automation, medical equipment, and marine systems – the confidence to adopt the CAN bus for their communication needs.
- Continuous Evolution: The ISO 11898 series has seen revisions and updates over the years, reflecting the evolving needs of industries and advancements in technology. For instance, the introduction of CAN FD (Flexible Data-Rate) by Bosch was later incorporated into the ISO standard, ensuring that the protocol remained relevant and up-to-date.
The ISO standardization of the CAN bus was a pivotal moment in the technology’s journey. It provided a consistent framework that industries could rally around, ensuring that the CAN bus realized its full potential as a robust, reliable, and efficient communication protocol. The collaborative efforts of organizations like ISO and innovators like Bosch underscore the importance of standardization in driving technological progress.
Modern Day Applications and Evolution
From its inception in the 1980s as a solution to automotive wiring challenges, the CAN bus has evolved significantly, finding applications in a myriad of industries and continuously adapting to the ever-changing technological landscape.
Beyond Automotive: Diverse Applications
While the automotive sector remains a primary user of the CAN bus, its robustness and efficiency have made it attractive to various other industries:
- Industrial Automation: In factories and manufacturing units, the CAN bus connects sensors, actuators, and controllers, facilitating real-time monitoring and control of machinery and processes.
- Medical Equipment: Devices like patient monitors, infusion pumps, and diagnostic machines use the CAN bus to relay information and ensure synchronized operation.
- Marine Systems: Modern ships and boats incorporate the CAN bus for navigation, engine management, and onboard entertainment systems.
- Agriculture: Tractors, harvesters, and other agricultural machinery utilize the CAN bus for precision farming, ensuring optimal use of resources and maximizing yields.
- Aerospace: Some aircraft systems employ the CAN bus for non-critical communications, given its reliability and fault tolerance.
Evolutionary Milestones
The CAN bus has seen several evolutionary milestones that have ensured its continued relevance:
- CAN 2.0B: Introduced in the 1990s, this extension allowed for longer message identifiers, enhancing the system’s capabilities.
- CAN FD (Flexible Data-Rate): Launched by Bosch in 2012, CAN FD addressed the increasing data demands of modern systems by allowing for faster data transmission rates than the classic CAN.
- Time-Triggered CAN (TTCAN): This variant of the CAN bus introduced time-triggered communication, enabling more deterministic data exchanges, crucial for applications that require precise synchronization.
- CANopen and DeviceNet: These are higher-layer protocols built on top of the standard CAN protocol, offering predefined communication objects for various applications, from industrial machinery to medical equipment.
Challenges and Adaptations
With the proliferation of connected devices and the advent of the Internet of Things (IoT), the data traffic on networks like the CAN bus has surged. This has posed challenges like potential bottlenecks and the need for enhanced security measures. The industry has responded with innovations like:
- Enhanced Security: With connected vehicles and industrial systems becoming potential targets for cyber-attacks, there’s a growing emphasis on securing CAN bus communications through encryption and other security protocols.
- Integration with Modern Protocols: As industries adopt newer communication protocols, there’s a push to ensure that the CAN bus can seamlessly integrate with these systems, ensuring continued interoperability.
The modern-day applications and evolution of the CAN bus underscore its adaptability and enduring relevance. From cars to factories and fields, the CAN bus continues to facilitate reliable and efficient communication between devices. Its journey from a solution to automotive challenges to a cornerstone of modern communication networks is a testament to its robust design and the industry’s commitment to continuous innovation.
Technical Specifications
The CAN bus, with its message-based protocol, has been designed meticulously to ensure robust communication in environments prone to electrical noise, such as automotive settings. This section delves into the technical intricacies of the CAN bus, providing a comprehensive overview of its specifications and how they contribute to its efficiency and reliability.
Physical Layer
The physical layer of any communication protocol, including the CAN bus, refers to the tangible components and the electrical characteristics that facilitate data transmission. In the context of the CAN bus, the physical layer is crucial for ensuring reliable communication, especially given the electrically noisy environments in which it often operates, such as automotive and industrial settings.
Differential Signaling
- Concept: Differential signaling is the method by which the CAN bus transmits data. Instead of sending a single signal, the CAN bus sends two complementary signals across two wires: CAN_H (High) and CAN_L (Low).
- Advantages: This approach offers several benefits:
- Noise Immunity: Common electrical noise that might affect both wires equally gets canceled out when the difference between the signals is calculated, ensuring data integrity.
- Reliability: Even if one wire were to fail, the other could still transmit data, albeit at a reduced reliability.
- Voltage Flexibility: Differential signaling allows for lower voltage levels, which can be beneficial for power conservation.
Termination Resistors
- Purpose: Termination resistors are used at both ends of the CAN bus to match the impedance of the network. This prevents signal reflections, which can cause interference and data corruption.
- Typical Values: The standard value for these resistors is 120 ohms for high-speed CAN networks.
Voltage Levels and States
- Recessive State (Logical High): In this state, both CAN_H and CAN_L are at approximately the same voltage, typically around 2.5V. The bus is considered “idle” in this state.
- Dominant State (Logical Low): When a device transmits a dominant bit, the voltage on CAN_H rises (typically to around 3.5V) while the voltage on CAN_L drops (typically to around 1.5V). The dominant state has priority over the recessive state; if two devices transmit simultaneously, the dominant state will “override” the recessive state.
Connectors and Cabling
- Standard Cables: The CAN bus typically uses twisted-pair cabling, which further enhances noise immunity. The twisting helps ensure that any electrical interference affects both wires equally, allowing for effective noise cancellation.
- Connectors: While there isn’t a single standardized connector for the CAN bus, some common types include the 9-pin D-sub connector and OBD-II connector in automotive applications.
Ground Reference
For the differential voltage levels to be interpreted correctly by receiving nodes, a common ground reference is essential. All devices on the CAN network are typically connected to a common ground.
The physical layer of the CAN bus is a testament to thoughtful engineering aimed at ensuring robust and reliable communication. From the use of differential signaling to the incorporation of termination resistors, every aspect has been designed to optimize data transmission, even in challenging environments.
Data Link Layer
The Data Link Layer is a crucial component of the CAN bus protocol, responsible for the reliable transmission and reception of data frames between nodes on the network. It ensures that messages are correctly framed, transmitted, received, and acknowledged, while also handling any potential conflicts or errors that might arise during communication.
Frame Structuring
The Data Link Layer is responsible for structuring data into frames for transmission. A typical CAN frame consists of several fields:
- Start of Frame (SOF): A single dominant bit indicating the beginning of a new frame.
- Arbitration Field: Contains the identifier which determines the message’s priority. A lower identifier value indicates a higher priority.
- Control Field: Specifies the length of the data field, indicating how many bytes of data the frame contains.
- Data Field: Contains the actual data being transmitted, which can be anywhere from 0 to 8 bytes for standard CAN frames.
- CRC Field: Contains a Cyclic Redundancy Check value for error-checking purposes.
- Acknowledgment (ACK) Field: A slot where receivers can acknowledge the successful reception of a frame.
- End of Frame (EOF): A series of recessive bits indicating the end of the frame.
Arbitration
Arbitration is the process that determines which message gets transmitted when multiple nodes attempt to send messages simultaneously:
- Non-destructive Arbitration: If two nodes start transmitting at the same time, the node with the higher priority (lower identifier) will continue its transmission, while the other node will stop and wait. This process ensures that high-priority messages are transmitted first without corrupting the data.
Acknowledgment Mechanism
After a message is transmitted, receiving nodes check the message for errors:
- Positive Acknowledgment: If the message is error-free, the receiving node will send an acknowledgment by overwriting a specific bit in the ACK slot of the frame.
- Lack of Acknowledgment: If the transmitting node doesn’t receive an acknowledgment, it assumes the message was not received and will attempt to retransmit it.
Error Handling
The Data Link Layer has robust error detection and signaling mechanisms:
- Error Detection: Several methods, including CRC checks, frame format checks, and acknowledgment checks, are used to detect errors in transmitted messages.
- Error Signaling: If a node detects an error, it will immediately signal this to the rest of the network by transmitting an error frame. This ensures that erroneous messages are not propagated through the network.
- Automatic Retransmission: If a message encounters an error during transmission, the CAN protocol will automatically attempt to retransmit it.
Fault Confinement
The CAN protocol has mechanisms to identify faulty nodes and prevent them from disrupting network communication:
- Error Counters: Each node maintains two error counters: Transmit Error Counter (TEC) and Receive Error Counter (REC). These counters increase or decrease based on the node’s activities and the errors it detects or commits.
- Error States: Based on the error counters, a node can be in one of three states:
- Error Active: Normal operation state where the node can send and receive messages.
- Error Passive: Entered when either error counter exceeds a certain threshold. In this state, the node takes longer to signal errors and has restrictions on message transmission.
- Bus Off: If the transmit error counter exceeds a higher threshold, the node enters the “Bus Off” state, where it is effectively disconnected from the network. Manual or automatic mechanisms are required to bring the node back to the “Error Active” state.
The Data Link Layer of the CAN bus ensures that data transmission between nodes is reliable, efficient, and error-free. Through its mechanisms for frame structuring, arbitration, acknowledgment, error handling, and fault confinement, the CAN protocol provides a robust foundation for communication in various applications, from vehicles to industrial systems.
Bit Rates and Timing
Bit rates and timing are fundamental aspects of the CAN bus, ensuring synchronized and efficient communication across the network. Proper configuration of these parameters is crucial for the reliable operation of the CAN network, especially when multiple nodes are involved.
Bit Rates
The bit rate, often referred to as the baud rate, dictates how fast data is transmitted over the CAN bus. The CAN protocol supports a range of bit rates, but the actual rate used depends on several factors:
- Network Length: Longer networks typically require lower bit rates to ensure reliable communication due to increased signal propagation delays.
- Number of Nodes: A higher number of nodes can introduce more delays and require more arbitration, potentially affecting the optimal bit rate.
- Noise Environment: In electrically noisy environments, a lower bit rate might be chosen to enhance signal integrity and reliability.
Commonly used bit rates in the CAN bus include:
- High-speed CAN: Rates up to 1 Mbit/s are typical for networks with shorter cable lengths and are often used for critical systems like engine control modules in vehicles.
- Low-speed/Fault-tolerant CAN: Rates up to 125 Kbit/s are used for longer networks or less time-critical applications, such as door controls or interior lighting in vehicles.
Bit Timing Configuration
Bit timing in the CAN bus is more intricate than just setting a bit rate. It involves dividing the time taken to transmit one bit (bit time) into smaller segments. Proper configuration ensures synchronization between nodes:
- Synchronization Segment (Sync_Seg): This is the start of the bit time and is used to synchronize the nodes on the bus.
- Propagation Time Segment (Prop_Seg): Accounts for the physical delay introduced by the bus length and helps in compensating for it.
- Phase Buffer Segment 1 (Phase_Seg1) and Phase Buffer Segment 2 (Phase_Seg2): These segments provide additional time buffers to adjust for edge synchronization of the CAN bus signals.
The sum of these segments determines the overall bit time. For example, a bit rate of 500 Kbit/s would have a bit time of 2 microseconds.
Resynchronization
Given the asynchronous nature of the CAN bus, where each node has its own oscillator, slight drifts in timing can occur. To counteract this:
- Resynchronization Jumps: During each bit transmission, nodes can adjust their timing by making small “jumps” in the bit time, either advancing or delaying their internal clocks to stay synchronized with the bus.
- Edge Detection: Nodes detect the edges of transmitted bits to determine when resynchronization is needed.
Oscillator Tolerance
For the CAN bus to function reliably, the oscillators of all nodes must be within a certain tolerance. This ensures that even with slight variations in individual oscillator frequencies, the nodes remain sufficiently synchronized over time.
Bit rates and timing are foundational to the operation of the CAN bus. Proper configuration and understanding of these parameters ensure that all nodes on the network can communicate reliably and efficiently. Whether it’s choosing the right bit rate for a specific application or fine-tuning bit timing segments for optimal synchronization, these aspects play a pivotal role in the robust performance of the CAN network.
Message Structure
The CAN bus employs a specific message structure, often referred to as a “frame,” to facilitate communication between nodes. This structure ensures that data is transmitted, received, and interpreted consistently across all devices on the network. Understanding the CAN frame’s composition is essential for anyone working with or designing systems that utilize the CAN protocol.
Types of Frames
The CAN protocol defines several types of frames:
- Data Frame: Used to transmit data and control information.
- Remote Frame: Used to request data from another node.
- Error Frame: Signaled by any node that detects an error to alert other nodes on the bus.
- Overload Frame: Used to introduce a delay between successive data or remote frames, providing extra processing time for nodes.
For the purpose of this discussion, we’ll focus on the structure of the Data Frame, which is the most commonly used.
Data Frame Structure
A standard CAN Data Frame consists of the following fields:
- Start of Frame (SOF):
- A single dominant bit that indicates the beginning of a new frame.
- Used for synchronization, allowing all nodes to align their internal clocks.
- Arbitration Field:
- Contains the message’s identifier, determining its priority.
- Standard CAN (CAN 2.0A) uses an 11-bit identifier.
- Extended CAN (CAN 2.0B) uses a 29-bit identifier, which includes an 18-bit extension to the standard 11-bit identifier.
- Also contains the Remote Transmission Request (RTR) bit, which differentiates between data frames and remote request frames.
- Control Field:
- Specifies the number of bytes in the data field, ranging from 0 to 8 bytes.
- Contains other control bits, including the Identifier Extension (IDE) bit, which indicates whether the frame is using the standard or extended format.
- Data Field:
- Contains the actual data being transmitted.
- The length is determined by the control field and can be up to 8 bytes for standard CAN frames.
- CRC Field:
- Contains a Cyclic Redundancy Check value, ensuring error-free transmission.
- Nodes that receive the frame will compute their own CRC from the received data and compare it to this field to detect any discrepancies.
- Acknowledgment (ACK) Field:
- Comprises one slot bit and one delimiter bit.
- Transmitting nodes listen during the ACK slot to determine if at least one other node on the network received the frame without errors.
- End of Frame (EOF):
- Consists of seven recessive bits, indicating the end of the frame.
- Ensures a minimum gap between consecutive frames, allowing nodes to prepare for the next frame or signal errors.
- Interframe Space:
- A period of three recessive bits following the EOF.
- Allows for error frames or overload frames to be transmitted before the next data or remote frame.
The CAN bus message structure is meticulously designed to ensure robust and efficient communication across the network. Each field in the frame serves a specific purpose, from prioritizing messages through the arbitration field to ensuring data integrity with the CRC field. This structured approach is a testament to the CAN protocol’s reliability, making it a preferred choice for critical applications in automotive, industrial, and many other sectors.
Error Handling
One of the standout features of the CAN bus protocol is its robust error handling capabilities. Given the critical nature of many CAN-based systems, especially in automotive and industrial applications, ensuring data integrity and reliable communication is paramount. The CAN protocol incorporates multiple mechanisms to detect, signal, and recover from errors, ensuring that the network remains reliable even in challenging conditions.
Types of Errors
The CAN protocol classifies errors into several categories:
- Bit Error: Occurs when a transmitting node detects a discrepancy between the transmitted bit and the bit read from the bus.
- Stuff Error: The CAN protocol employs bit-stuffing to ensure synchronization. After five consecutive bits of the same value, a node will insert (or “stuff”) a bit of the opposite value. A stuff error occurs when this expected stuffed bit is not detected.
- CRC Error: After the data field in a CAN frame, a Cyclic Redundancy Check (CRC) sequence is sent. Receiving nodes compute the CRC of the received data and compare it to the transmitted CRC. A mismatch indicates a CRC error.
- Form Error: Occurs when a fixed-form field (like the EOF field) deviates from its expected format.
- Acknowledgment Error: If a transmitting node does not detect any dominant bits in the acknowledgment slot of a frame, it assumes that the frame was not received by any node and flags an acknowledgment error.
Error Signaling
When a node detects an error, it immediately signals this to the entire network:
- Error Flag: A sequence of six dominant bits, used to indicate an error. This flag disrupts the normal flow of data on the bus, ensuring that all nodes detect the error.
- Error Delimiter: After the error flag, an error delimiter consisting of eight recessive bits is transmitted.
Error Counters and Confinement
Each node on the CAN network maintains two error counters:
- Transmit Error Counter (TEC): Incremented when the node detects an error while transmitting, and decremented when the node successfully transmits a message.
- Receive Error Counter (REC): Incremented when the node detects an error while receiving, and decremented when a message is successfully received without errors.
Based on these counters, a node can be in one of three error states:
- Error Active: The default state when both TEC and REC are below a threshold (usually 128). In this state, the node can actively participate in bus communication and signal errors.
- Error Passive: Entered when either TEC or REC exceeds the threshold. In this state, the node still participates in bus communication but becomes less aggressive in error signaling, using passive error flags (six recessive bits).
- Bus Off: If the TEC surpasses a higher threshold (usually 256), the node enters the “Bus Off” state. In this state, the node is effectively disconnected from the network and will not participate in any bus communication. Manual intervention or a predefined recovery mechanism is required to reset the node to the “Error Active” state.
Automatic Retransmission
One of the key features of the CAN protocol is its ability to automatically retransmit messages that encounter errors. If a node detects an error in its transmitted message (e.g., through a missing acknowledgment or a CRC mismatch), it will schedule the message for retransmission. This ensures that transient errors, perhaps due to temporary electrical noise, do not result in data loss.
Error handling is a cornerstone of the CAN bus protocol, ensuring that communication remains reliable even in the face of external disturbances or internal node failures. Through its comprehensive error detection, signaling, and recovery mechanisms, the CAN protocol provides a robust communication backbone for a wide range of critical applications.
Limitations and Maximums
While the CAN bus is renowned for its robustness and efficiency, like any technology, it has its limitations. Understanding these constraints is essential for designers and engineers to ensure optimal performance and avoid potential pitfalls when implementing CAN-based systems.
1. Cable Length vs. Bit Rate
The maximum cable length of a CAN network is inversely proportional to the bit rate:
- High-speed CAN (1 Mbit/s): The maximum cable length is approximately 40 meters.
- Medium-speed CAN (500 Kbit/s): The maximum length can be up to 100 meters.
- Low-speed CAN (125 Kbit/s): Can extend up to 500 meters or more.
These values can vary based on the specific physical layer implementation and the quality of the cabling used. The primary reason for this limitation is the signal propagation delay, which can lead to synchronization issues at higher bit rates over longer distances.
2. Maximum Nodes
The number of nodes that can be connected to a single CAN bus is theoretically limited by the electrical loading of the bus (due to each node’s transceiver) and practical considerations related to bit timing and synchronization:
- A typical high-speed CAN bus can support up to 110 nodes. However, this number can vary based on the specific transceivers used and the network’s bit rate.
3. Data Throughput
While CAN bit rates can reach up to 1 Mbit/s, the actual data throughput is lower due to factors like:
- Overhead from non-data bits in the CAN frame (e.g., SOF, CRC, EOF).
- Time gaps between frames.
- Bus idle time and the potential retransmission of frames due to errors.
For instance, at 1 Mbit/s with an average payload of 8 bytes per frame, the actual data throughput might be closer to 800 Kbit/s or less.
4. Data Length
A standard CAN frame can transmit a maximum of 8 bytes of data. While this is sufficient for many applications, it can be limiting for systems that require the transmission of larger data packets. Solutions include:
- Splitting larger data sets into multiple CAN frames.
- Using protocols like CANopen or J1939, which define methods for transmitting larger data blocks.
5. Latency
Due to the arbitration mechanism, where messages with lower identifier values have higher priority, the latency for transmitting a message can vary. In a busy network with many high-priority messages, lower-priority messages might experience significant delays.
6. Error Recovery Time
In scenarios where a node enters the “Bus Off” error state, there can be a significant delay before it can rejoin the network, especially if manual intervention is required.
7. Security
Traditional CAN does not have built-in security features, making it vulnerable to potential cyber-attacks. While newer adaptations of CAN (like CAN FD) and higher-layer protocols are addressing this, security remains a concern for many CAN-based systems.
While the CAN bus offers numerous advantages, being aware of its limitations and maximums is crucial for effective system design. By understanding these constraints and employing best practices or supplementary protocols, designers can harness the full potential of the CAN bus while mitigating potential challenges.
Other Applications of CAN bus
The Controller Area Network (CAN) bus, since its inception, has found its way into a multitude of applications. Its robustness, efficiency, and real-time capabilities make it a preferred choice for various industries. This section delves into the diverse applications of the CAN bus, showcasing its versatility and widespread adoption.
Automotive Industry
The automotive industry was the birthplace of the CAN bus, and over the years, it has become an integral part of modern vehicles. As cars evolved from purely mechanical systems to complex integrations of mechanical and electronic components, there arose a need for a robust communication system to manage and coordinate these components. The CAN bus emerged as the solution, providing a reliable and efficient means of communication between the various electronic control units (ECUs) in a vehicle.
Evolution and Adoption
- Early Days: In the 1980s, as vehicles began incorporating more electronic functions, the amount of wiring required increased dramatically. This not only added weight but also complexity. The CAN bus was introduced by Bosch in 1986 as a way to reduce this complexity by allowing multiple ECUs to communicate over a single or dual-wire system.
- Standardization: The CAN protocol was standardized in 1993 as ISO 11898, which further accelerated its adoption across the automotive industry.
Key Applications in Vehicles
- Engine Control: The Engine Control Module (ECM) uses the CAN bus to gather data from various sensors like oxygen sensors, fuel injectors, and throttle position sensors. This data helps in optimizing engine performance, fuel efficiency, and emissions.
- Transmission Management: The Transmission Control Module (TCM) communicates with the ECM and other systems to ensure smooth gear shifts, optimize fuel efficiency, and protect the transmission from potential damage.
- Safety Systems:
- Anti-lock Braking System (ABS): Uses wheel speed sensors to prevent wheel lockup during braking.
- Electronic Stability Control (ESC): Monitors and controls the car’s stability, reducing the risk of skidding.
- Airbag Systems: Monitors sensors to determine when to deploy airbags in the event of a collision.
- Infotainment and Navigation: Modern infotainment systems use the CAN bus to display vehicle data, control multimedia playback, manage hands-free calls, and provide navigation guidance.
- Body Control: Manages functions like power windows, central locking, lighting, and climate control.
- Diagnostics: The On-Board Diagnostics (OBD) system uses the CAN bus to monitor vehicle performance and report issues. Mechanics can connect to the OBD port to retrieve fault codes and diagnose problems.
Advantages in Automotive Applications
- Weight Reduction: By reducing the amount of wiring, the CAN bus helps decrease vehicle weight, contributing to better fuel efficiency.
- Real-time Communication: The CAN bus’s real-time capabilities ensure that critical systems, like safety features, operate seamlessly and promptly.
- Flexibility: New features or updates can be added to vehicles without the need for significant rewiring or hardware changes.
- Fault Detection: The CAN protocol’s error-handling capabilities allow for quick detection and isolation of faults, ensuring system reliability.
Challenges and Future Trends
- Security Concerns: As vehicles become more connected, there are growing concerns about the security of CAN-based systems. Efforts are underway to develop more secure versions of the CAN protocol and implement additional security measures.
- Integration with New Technologies: With the rise of electric vehicles, autonomous driving, and vehicle-to-everything (V2X) communication, the CAN bus will need to integrate with new technologies and possibly coexist with other communication protocols.
The CAN bus has revolutionized the automotive industry, enabling the seamless integration of complex electronic systems that enhance vehicle performance, safety, and comfort. As the industry continues to evolve, the CAN bus will undoubtedly adapt and remain a cornerstone of automotive communication systems.
Industrial Automation
Industrial automation involves the use of control systems, such as computers or robots, for handling different processes and machinery in an industry to replace human intervention. The CAN bus, with its robustness and real-time capabilities, has become a pivotal component in the realm of industrial automation, facilitating seamless communication between various devices and systems.
Role in Industrial Automation
The CAN bus serves as the backbone for communication in many automated industrial setups. Its ability to function reliably in electrically noisy environments, coupled with its efficient data transmission capabilities, makes it ideal for industrial applications.
- Sensor Data Collection: In automated factories, numerous sensors continuously monitor parameters like temperature, pressure, humidity, and more. The CAN bus ensures that data from these sensors is reliably transmitted to control systems for analysis and action.
- Machine Control: The CAN bus connects programmable logic controllers (PLCs), motor drives, and actuators, ensuring synchronized operations. For instance, in an assembly line, it can coordinate the actions of multiple robots to ensure efficient production.
- Diagnostics and Monitoring: Industrial setups utilize the CAN bus for real-time monitoring of equipment. This aids in predictive maintenance, where potential issues are identified and addressed before they lead to equipment failure.
- Safety Systems: In industries where safety is paramount, the CAN bus manages safety equipment like emergency shut-offs, alarms, and fire suppression systems.
Advantages in Industrial Settings
- Reliability: The CAN bus is designed to operate reliably in harsh environments, making it resistant to electrical interference commonly found in industrial settings.
- Scalability: As industrial processes evolve and expand, more devices can be easily added to the existing CAN network without significant overhauls.
- Cost-Efficiency: By reducing the amount of wiring and facilitating efficient communication, the CAN bus can lead to cost savings in both installation and operation.
- Real-time Operation: The deterministic nature of the CAN bus ensures timely responses, which is crucial for processes that require real-time control and monitoring.
Challenges in Industrial Automation
- Bandwidth Limitations: High-speed industrial processes might require faster data rates than what the standard CAN bus offers. This has led to the exploration of other protocols or the use of CAN FD (Flexible Data-rate), an extension of the standard CAN protocol that offers higher data rates.
- Complex Network Topologies: Large industrial setups might have complex network topologies that can challenge the traditional linear or star configurations of the CAN bus.
- Security: As with other applications, the security of CAN-based systems in industrial settings is a concern, especially with the rise of Industry 4.0 and increased connectivity.
Integration with Other Protocols
In many industrial settings, the CAN bus operates alongside other communication protocols:
- CANopen: An open protocol based on CAN, specifically designed for embedded systems in automation. It defines higher layers of the OSI model and is commonly used in various industrial applications.
- DeviceNet: Built on the CAN bus, DeviceNet is used for industrial control applications, allowing devices like sensors and actuators to communicate with controllers.
The CAN bus has firmly established its presence in the world of industrial automation, driving efficiency, reliability, and precision in various processes. As the industrial landscape continues to evolve with advancements like the Internet of Things (IoT) and artificial intelligence, the role of the CAN bus will undoubtedly adapt, further cementing its importance in the future of automation.
Medical Devices
The medical industry, with its emphasis on precision, reliability, and safety, demands communication systems that can meet these stringent requirements. The CAN bus, known for its robustness and real-time capabilities, has found its way into various medical devices and systems, ensuring seamless and reliable operations.
Role in Medical Devices
The integration of the CAN bus in medical devices has enhanced their functionality, reliability, and interoperability:
- Patient Monitoring Systems: Modern hospitals use centralized patient monitoring systems where multiple devices (like heart rate monitors, blood pressure machines, and pulse oximeters) send data to a central station. The CAN bus facilitates this communication, ensuring real-time updates and alerts.
- Medical Imaging: Devices like MRI machines, CT scanners, and X-ray machines have multiple components that need to communicate synchronously. The CAN bus aids in coordinating these components, ensuring high-quality imaging.
- Robotic Surgery: Surgical robots, which offer high precision and minimally invasive procedures, rely on the CAN bus for coordinating the movement of robotic arms, cameras, and surgical instruments.
- Infusion Pumps: These devices, which deliver fluids, nutrients, or medications into a patient’s body in controlled amounts, use the CAN bus to monitor and adjust the flow rates based on feedback from sensors.
- Dialysis Machines: The CAN bus ensures that these machines operate efficiently, monitoring various parameters like blood flow rate, temperature, and pressure.
Advantages in Medical Applications
- Reliability: Given the critical nature of medical applications, the robust error-handling capabilities of the CAN bus ensure that devices operate reliably, minimizing risks to patients.
- Real-time Operation: Many medical procedures and devices require real-time responses. The deterministic nature of the CAN bus ensures timely data transmission and device coordination.
- Interoperability: With standardized communication, devices from different manufacturers can communicate seamlessly, enhancing the flexibility and efficiency of medical setups.
- Scalability: As medical facilities grow or upgrade, new devices can be easily integrated into the existing CAN network.
Challenges in Medical Applications
- Data Security: Patient data is sensitive, and any communication system, including the CAN bus, needs to ensure that this data is secure from potential breaches or unauthorized access.
- Complexity: Medical devices can be intricate, and integrating the CAN bus requires expertise to ensure that the system meets all medical standards and regulations.
- Bandwidth: High-resolution medical imaging devices or systems that transmit large amounts of data might require higher bandwidths than what the standard CAN bus offers.
Integration with Other Systems
In many medical setups, the CAN bus might operate alongside other communication protocols or systems:
- Hospital Information Systems (HIS): The CAN bus can interface with broader hospital information systems, ensuring that patient data from devices is integrated into electronic health records.
- Wireless Communication: In some applications, the CAN bus might be integrated with wireless communication systems, offering flexibility in device placement and data access.
The integration of the CAN bus in medical devices underscores the protocol’s versatility and reliability. In an industry where precision and patient safety are paramount, the CAN bus offers a communication backbone that meets these demands. As medical technology continues to advance, the role of the CAN bus is set to expand, further enhancing the capabilities and efficiency of medical devices and systems.
Aerospace and Aviation
The aerospace and aviation sectors are characterized by their emphasis on safety, precision, and reliability. As aircraft systems have become more complex and integrated, there’s been a growing need for efficient communication protocols. The CAN bus, with its robust error-handling and real-time capabilities, has been increasingly adopted in aerospace applications, complementing or even replacing older avionic data buses.
Role in Aerospace and Aviation
The CAN bus serves various functions in both civil and military aircraft:
- Avionics Systems: Modern aircraft are equipped with numerous avionic systems, from navigation and communication to flight control systems. The CAN bus facilitates communication between these systems, ensuring synchronized operations.
- Sensor Data Collection: Aircraft have a multitude of sensors monitoring parameters like altitude, airspeed, temperature, and engine performance. The CAN bus ensures timely and reliable transmission of this data to relevant systems and displays.
- Actuator Control: Actuators control various aircraft components, from control surfaces like ailerons and flaps to landing gear. The CAN bus coordinates the operation of these actuators based on inputs from the flight control system.
- Maintenance and Diagnostics: Modern aircraft have sophisticated diagnostic systems that monitor the health of various components. The CAN bus aids in collecting this data, which can be used for predictive maintenance and troubleshooting.
- Cabin Systems: The CAN bus manages various cabin systems, including lighting, entertainment, and climate control, enhancing passenger comfort.
Advantages in Aerospace Applications
- Weight Reduction: Traditional avionic systems required extensive wiring, adding significant weight to the aircraft. The CAN bus reduces this wiring complexity, leading to weight savings and, consequently, fuel efficiency.
- Reliability: The aerospace environment is challenging, with factors like temperature fluctuations, vibration, and electromagnetic interference. The CAN bus’s robust design ensures reliable communication in these conditions.
- Real-time Operation: Many aerospace systems, especially flight controls, require real-time responses. The CAN bus’s deterministic nature meets this requirement.
- Scalability: As aircraft systems evolve, the CAN bus allows for easy integration of new devices or upgrades to existing ones.
Challenges in Aerospace Applications
- Certification and Standards: Aerospace applications have stringent certification requirements. Any CAN-based system needs to meet these standards, which can be a lengthy and costly process.
- Data Security: With the rise of connected aircraft and the potential for cyber threats, ensuring the security of CAN-based communication systems is paramount.
- Integration with Legacy Systems: Many aircraft still operate with older avionic systems. Integrating the CAN bus with these systems can be complex.
Integration with Other Avionic Buses
While the CAN bus is gaining traction in aerospace, it often operates alongside or integrates with other avionic data buses:
- ARINC 429: A widely-used data bus in commercial aviation. While it’s point-to-point and has a slower data rate compared to CAN, it’s still prevalent in many aircraft systems.
- MIL-STD-1553: A military standard avionic bus used in many defense platforms. Like ARINC 429, it’s point-to-point and has been in use for decades.
The adoption of the CAN bus in aerospace and aviation underscores the protocol’s adaptability and reliability. In an environment where safety and precision are of utmost importance, the CAN bus offers a communication solution that meets the industry’s stringent demands. As aerospace technology continues to advance, the role of the CAN bus is set to grow, further enhancing the capabilities and safety of aircraft systems.
Marine Systems
The marine environment presents a unique set of challenges, from the corrosive nature of saltwater to the dynamic conditions of the open sea. Marine systems, whether on commercial vessels, naval ships, or recreational boats, require robust and reliable communication networks. The CAN bus, with its inherent resilience and efficiency, has become a preferred choice for various marine applications.
Role in Marine Systems
The CAN bus serves a multitude of functions aboard marine vessels:
- Engine Monitoring and Control: Modern marine engines, whether diesel or gasoline-powered, are equipped with electronic control units (ECUs). The CAN bus facilitates communication between these ECUs and various sensors, ensuring optimal engine performance, fuel efficiency, and emissions control.
- Navigation Systems: The CAN bus integrates GPS units, sonar systems, radar, and other navigation aids, providing real-time data to the vessel’s helm for safe and efficient navigation.
- Autopilot Systems: Modern vessels often employ autopilot systems for long voyages. The CAN bus ensures that these systems receive accurate data from sensors and navigation systems, allowing for automated course adjustments and steering.
- Safety Systems: From fire suppression systems to bilge pumps, the CAN bus manages various safety equipment on board, ensuring timely responses to emergencies.
- Entertainment and Cabin Systems: On luxury yachts and cruise ships, the CAN bus might be used to manage entertainment systems, lighting, climate control, and other cabin amenities.
Advantages in Marine Applications
- Reliability in Harsh Conditions: The marine environment can be electrically noisy, with interference from engines, radios, and other equipment. The CAN bus’s design ensures reliable communication even in these challenging conditions.
- Reduced Wiring Complexity: Traditional marine systems required extensive cabling, which could be cumbersome and prone to corrosion. The CAN bus simplifies this, leading to easier installations and maintenance.
- Scalability: As marine technology evolves, the CAN bus allows for easy integration of new devices or systems, ensuring vessels remain up-to-date.
- Real-time Operation: For safety-critical systems like navigation and engine control, real-time data transmission is essential. The CAN bus’s deterministic nature ensures timely communication between devices.
Challenges in Marine Applications
- Corrosion Resistance: The marine environment, especially saltwater, is corrosive. While the CAN bus reduces wiring, the connectors, cables, and devices used must be corrosion-resistant, which can increase costs.
- Integration with Legacy Systems: Older vessels might operate with dated systems. Integrating the CAN bus with these systems can be complex and might require custom solutions.
- Security: With the rise of connected marine systems, ensuring the security of CAN-based communication networks against potential cyber threats becomes crucial.
Integration with Other Marine Protocols
While the CAN bus is gaining popularity in marine applications, it often operates alongside or integrates with other marine communication protocols:
- NMEA 2000: A marine communication standard based on the CAN bus. It defines how data is transmitted across the network and ensures interoperability between devices from different manufacturers.
- NMEA 0183: An older marine communication standard that uses a simple ASCII serial communications protocol. While being phased out in favor of NMEA 2000, it’s still found on many vessels.
The integration of the CAN bus in marine systems highlights the protocol’s versatility across diverse environments. In a setting where safety, reliability, and performance are paramount, the CAN bus offers a communication backbone that meets the marine industry’s demands. As marine technology continues to advance, the role of the CAN bus is set to expand, further enhancing the capabilities and safety of marine systems.
Agriculture and Forestry
The agriculture and forestry sectors have witnessed significant technological advancements over the past few decades. Modern machinery and equipment, designed to enhance productivity and efficiency, rely heavily on electronic systems for operation and monitoring. The CAN bus, with its robust communication capabilities, has emerged as a vital component in the modernization of these sectors.
Role in Agriculture and Forestry
The CAN bus plays a pivotal role in various agricultural and forestry applications:
- Precision Farming: Precision agriculture involves the use of technology to enhance farming efficiency and crop yield. The CAN bus connects sensors that monitor soil conditions, weather data, and crop health, allowing for targeted interventions like precise irrigation, fertilization, and pest control.
- Tractor and Machinery Control: Modern tractors and harvesters are equipped with numerous electronic control units (ECUs) that manage functions like engine performance, transmission, and implement control. The CAN bus facilitates communication between these ECUs, ensuring coordinated and efficient operations.
- Forestry Equipment: Machines used in forestry, like loggers and skidders, rely on the CAN bus for functions such as boom control, load sensing, and terrain navigation.
- Diagnostics and Monitoring: The CAN bus aids in real-time monitoring of equipment health, fuel levels, and operational parameters. This data is crucial for predictive maintenance, ensuring that machinery is always in optimal working condition.
- Automated Systems: With the rise of autonomous farming and forestry equipment, the CAN bus ensures that these machines receive accurate data from sensors and navigation systems, allowing for automated operations.
Advantages in Agricultural and Forestry Applications
- Efficiency and Productivity: The CAN bus enables real-time monitoring and control of machinery, leading to optimized operations, reduced fuel consumption, and increased productivity.
- Reliability: Given the challenging conditions of farms and forests, the robust design of the CAN bus ensures reliable communication, minimizing downtime and operational disruptions.
- Scalability: As farming and forestry practices evolve, the CAN bus allows for easy integration of new sensors, implements, or systems.
- Cost Savings: By optimizing operations and reducing wastage, the CAN bus can lead to significant cost savings in both agriculture and forestry.
Challenges in Agricultural and Forestry Applications
- Harsh Environments: Farms and forests can be dusty, muddy, and wet. Ensuring that CAN bus components are protected from these elements is crucial.
- Integration with Legacy Systems: Older machinery might not be equipped with modern electronic systems. Integrating the CAN bus with these machines can be complex and might require custom solutions.
- Training and Adoption: Introducing advanced electronic systems in traditional sectors like agriculture and forestry requires training personnel to understand and operate these systems effectively.
Integration with Other Agricultural Protocols
While the CAN bus is foundational, it often operates alongside or integrates with specific agricultural communication protocols:
- ISOBUS: An international standard for communication in agriculture, ISOBUS ensures that tractors and implements from different manufacturers can communicate seamlessly. It’s built on the CAN bus and defines additional layers and functions specific to agriculture.
The integration of the CAN bus in agriculture and forestry underscores the protocol’s adaptability and relevance in diverse sectors. In industries that form the backbone of global food and resource supply, the CAN bus enhances efficiency, safety, and sustainability. As technology continues to reshape agriculture and forestry, the role of the CAN bus is set to grow, further driving innovation and progress in these vital sectors.
Public Transportation
Public transportation systems, encompassing buses, trams, trains, and more, play a crucial role in urban mobility and sustainability. As these systems evolve to meet the demands of growing urban populations and environmental concerns, the need for efficient communication networks within these vehicles becomes paramount. The CAN bus, renowned for its robustness and real-time capabilities, has been increasingly adopted in public transportation applications.
Role in Public Transportation
The CAN bus serves a multitude of functions in various public transportation vehicles:
- Vehicle Management Systems: Modern public transportation vehicles, especially buses and trams, are equipped with electronic control units (ECUs) that manage engine performance, transmission, and braking systems. The CAN bus facilitates communication between these ECUs, ensuring optimal vehicle performance and fuel efficiency.
- Passenger Information Systems: The CAN bus manages displays and announcement systems that provide passengers with real-time information about routes, stops, and schedules.
- Safety Systems: Public transportation vehicles are equipped with safety features like anti-lock braking systems (ABS), electronic stability control, and emergency braking systems. The CAN bus ensures that these systems communicate seamlessly and respond promptly in critical situations.
- Fare Collection: Automated ticketing and fare collection systems in buses and trams can be managed via the CAN bus, ensuring accurate fare calculation and data transmission to central systems.
- Diagnostics and Monitoring: The CAN bus aids in real-time monitoring of vehicle health, fuel levels, and operational parameters. This data is crucial for predictive maintenance, ensuring that vehicles are always in optimal working condition and minimizing service disruptions.
- Climate Control: In larger vehicles like buses and trams, the CAN bus manages climate control systems, ensuring passenger comfort.
Advantages in Public Transportation Applications
- Efficiency: The CAN bus enables real-time monitoring and control of public transportation vehicles, leading to optimized operations, reduced fuel consumption, and timely services.
- Reliability: Given the critical nature of public transportation in urban settings, the robust design of the CAN bus ensures reliable communication, minimizing service disruptions and enhancing passenger safety.
- Cost Savings: By optimizing operations, reducing maintenance downtime, and enhancing fuel efficiency, the CAN bus can lead to significant cost savings for public transportation operators.
- Integration: The CAN bus allows for easy integration of new systems or upgrades, ensuring that public transportation vehicles remain up-to-date with the latest technologies.
Challenges in Public Transportation Applications
- Data Security: With the rise of connected transportation systems and the potential for cyber threats, ensuring the security of CAN-based communication networks becomes crucial.
- Complex Network Topologies: Large public transportation vehicles, especially trains, might have complex network topologies that challenge the traditional configurations of the CAN bus.
- Integration with Citywide Systems: Public transportation vehicles often need to communicate with broader citywide systems for traffic management, scheduling, and route optimization. Ensuring seamless integration between the CAN bus and these systems can be complex.
Integration with Other Transportation Protocols
While the CAN bus is foundational in many public transportation vehicles, it often operates alongside or integrates with specific transportation communication protocols:
- Train Communication Network (TCN): A standard for communication in trains, TCN ensures that different train components, from locomotives to passenger cars, communicate seamlessly. The CAN bus often forms a part of this network, especially in the Multifunction Vehicle Bus (MVB) segment of TCN.
The integration of the CAN bus in public transportation highlights the protocol’s versatility and capability to enhance urban mobility. In an era where efficient, reliable, and sustainable transportation is vital for urban growth and environmental sustainability, the CAN bus offers a communication solution that meets these demands. As public transportation systems continue to evolve with advancements in technology and urban planning, the role of the CAN bus is set to expand, further driving innovation and progress in urban mobility.
Home Automation
Home automation, often referred to as “smart home” technology, involves the control and automation of lighting, heating, ventilation, air conditioning, security, and other home appliances. As homes become smarter and more interconnected, there’s a growing need for efficient and reliable communication systems. The CAN bus, known for its robustness in automotive and industrial settings, is also finding its place in the realm of home automation.
Role in Home Automation
The CAN bus can serve various functions in a smart home environment:
- Lighting Control: The CAN bus can manage and coordinate lighting systems, allowing for scenarios like mood lighting, automated dimming, or lights that adjust based on natural daylight.
- HVAC Systems: Modern heating, ventilation, and air conditioning systems can be controlled via the CAN bus, ensuring optimal temperatures and air quality while optimizing energy consumption.
- Security Systems: The CAN bus integrates various security components, from cameras and motion sensors to door locks and alarm systems, providing a comprehensive security solution.
- Home Entertainment: Audio and video systems, including multi-room setups, can be managed via the CAN bus, allowing for synchronized playback or individual room controls.
- Appliance Management: The CAN bus can integrate with smart appliances, such as refrigerators, ovens, or washing machines, providing status updates, remote control, and energy management.
- Energy Monitoring: Smart homes often incorporate energy monitoring systems that track electricity, water, and gas consumption. The CAN bus facilitates communication between these systems and other home devices, enabling energy-saving scenarios.
Advantages in Home Automation Applications
- Centralized Control: The CAN bus allows for a centralized control mechanism, where homeowners can manage all connected devices from a single interface, be it a wall-mounted panel, a smartphone app, or voice commands.
- Reliability: Given its origins in critical applications like automotive and industrial systems, the CAN bus offers a high degree of reliability, ensuring that home automation systems function seamlessly.
- Scalability: As homeowners add more devices or upgrade existing ones, the CAN bus allows for easy integration, ensuring that the home automation system remains future-proof.
- Energy Efficiency: By coordinating various home systems, from lighting to HVAC, the CAN bus can optimize energy consumption, leading to cost savings and a reduced carbon footprint.
Challenges in Home Automation Applications
- Interoperability: The home automation market has various manufacturers and protocols. Ensuring that all devices, regardless of the manufacturer, communicate seamlessly over the CAN bus can be challenging.
- Data Security: Smart homes collect and transmit a lot of data. Ensuring the security of CAN-based communication networks against potential cyber threats is crucial.
- Complex Setups: While the CAN bus simplifies communication, setting up a comprehensive home automation system can still be complex and might require professional installation and configuration.
Integration with Other Home Automation Protocols
While the CAN bus offers a robust communication backbone, it often operates alongside or integrates with other home automation protocols:
- Zigbee and Z-Wave: These are popular wireless communication protocols for home automation. A smart home might use the CAN bus for wired devices and Zigbee or Z-Wave for wireless ones.
- Wi-Fi and Bluetooth: Many smart home devices connect via Wi-Fi or Bluetooth. Integrating these devices with a CAN-based system might require gateways or bridges.
The integration of the CAN bus in home automation underscores the protocol’s adaptability across a wide range of applications. In a setting where convenience, efficiency, and sustainability are paramount, the CAN bus offers a communication solution that meets these demands. As smart home technology continues to evolve and gain popularity, the role of the CAN bus is set to grow, further enhancing the capabilities and user experience of home automation systems.
The diverse applications of the CAN bus underscore its adaptability and effectiveness in ensuring reliable communication across various domains. From cars to factories, hospitals to fields, the CAN bus has proven its mettle, becoming an indispensable tool in modern electronics and communication systems.
Advantages and Limitations
The Controller Area Network (CAN) bus has been a revolutionary communication protocol in various industries, from automotive to home automation. While it offers numerous advantages, like any technology, it also has its limitations. This section delves into the strengths and constraints of the CAN bus.
-Advantages
Reliability
The Controller Area Network (CAN) bus is renowned for its reliability, especially in environments that are electrically noisy or challenging. This reliability has made it a preferred communication protocol in industries such as automotive, aerospace, and industrial automation. Let’s delve deeper into the factors that contribute to the CAN bus’s robustness.
Error Detection Mechanisms
One of the standout features of the CAN bus is its robust error detection capabilities. The protocol incorporates several mechanisms to ensure data integrity:
- Cyclic Redundancy Check (CRC): Every CAN message includes a CRC sequence, which is a mathematical checksum. Receivers calculate the CRC for the received message and compare it to the transmitted CRC. If there’s a mismatch, an error is flagged.
- Frame Check: The CAN protocol defines a specific format for message frames. If a receiving node detects any deviation from this format, it identifies it as an error.
- Acknowledgment Check: When a CAN node sends a message, it expects an acknowledgment from other nodes. If it doesn’t receive this acknowledgment, it assumes there was an error in transmission.
- Bit Monitoring: When a node sends a bit, it monitors the bus to verify that the bit’s value matches what was sent. If there’s a discrepancy, it’s treated as an error.
Fault Confinement
The CAN bus is designed to identify and isolate faulty nodes:
- Error Counters: Each node maintains two error counters – one for transmit errors and one for receive errors. When a node detects an error, the relevant counter is incremented. If either counter exceeds a predefined limit, the node transitions to an “error passive” state, reducing its impact on the bus.
- Bus Off State: If a node’s error counter continues to rise beyond a higher threshold, the node enters a “bus off” state, where it’s effectively disconnected from the bus. This ensures that a persistently faulty node doesn’t disrupt the entire network.
Redundancy
In critical applications, it’s common to implement redundant CAN networks. If one network fails, the backup can take over, ensuring uninterrupted communication. This redundancy enhances the overall reliability of the system.
Differential Signaling
The CAN bus uses differential signaling, where two complementary signals are transmitted over two separate wires. This approach reduces the impact of external electromagnetic interference, as any noise typically affects both wires equally and can be canceled out.
Physical Layer Standards
The physical layer of the CAN bus, which defines aspects like voltage levels and bit timing, is designed to be robust. For instance, the ISO 11898 standard specifies robust transceivers that can handle electrical disturbances common in automotive environments.
The reliability of the CAN bus is not accidental but a result of deliberate design choices aimed at ensuring data integrity and system robustness. These features, from advanced error detection mechanisms to fault confinement, make the CAN bus a trusted communication protocol in numerous applications where reliability is paramount. As industries continue to evolve and demand even more from communication networks, the foundational reliability of the CAN bus ensures it remains a cornerstone in the world of interconnected systems.
Real-time Communication
Real-time communication is essential in many industries, especially where timely responses can be the difference between smooth operation and potential disasters. The CAN (Controller Area Network) bus, with its deterministic nature, is designed to provide real-time communication capabilities, making it a preferred choice in sectors like automotive, aerospace, and industrial automation. Let’s explore the features and significance of the CAN bus’s real-time communication.
Deterministic Transmission
The CAN bus operates on a priority-based system, ensuring that messages with higher priority are transmitted before those with lower priority. This deterministic transmission is achieved through:
- Message Arbitration: When multiple nodes attempt to transmit messages simultaneously, the CAN bus uses a non-destructive arbitration method. Nodes monitor the bus and, if they detect a dominant bit when they’re sending a recessive bit, they stop transmitting, allowing the higher-priority message to proceed.
- Priority Encoding: The priority of a message is determined by its identifier. Lower identifier values have higher priority. This system ensures that critical messages are transmitted promptly.
Minimal Latency
The CAN bus’s arbitration method, combined with its efficient message framing, ensures minimal latency. Critical messages can be transmitted with predictable delays, which is vital for real-time applications.
Synchronization
The CAN protocol includes mechanisms to synchronize clocks of different nodes:
- Hard Synchronization: When a node starts to transmit, it resets its own clock and synchronizes with the start bit.
- Soft Synchronization: During message transmission, nodes adjust their clocks based on recessive-to-dominant or dominant-to-recessive edge transitions, ensuring that all nodes remain synchronized.
Time-Triggered CAN (TTCAN)
TTCAN is an extension of the standard CAN protocol, designed specifically for hard real-time requirements. It introduces a time-triggered communication mode, where messages are transmitted at predefined time slots. This ensures even more predictable and consistent message transmission times.
Real-time Data Handling
The CAN bus can handle real-time data from various sources:
- Sensors: In automotive applications, sensors monitoring parameters like speed, temperature, and fuel levels can transmit data in real-time, allowing for immediate responses.
- Actuators: In industrial automation, actuators need timely commands to operate machinery. The CAN bus ensures that these commands are delivered promptly.
- Safety Systems: In aerospace, real-time communication between flight control systems, navigation, and onboard sensors is crucial for safety.
The real-time communication capabilities of the CAN bus are a testament to its robust design and adaptability. In environments where milliseconds matter, the CAN bus ensures that data is transmitted and received with minimal and predictable delays. This real-time performance, combined with its other features like reliability and error handling, makes the CAN bus an indispensable tool in modern communication networks. As technology continues to advance and the demand for real-time data grows, the CAN bus stands poised to meet these challenges head-on.
Flexibility and Scalability
The CAN (Controller Area Network) bus is not just renowned for its reliability and real-time capabilities; its inherent flexibility and scalability have also made it a preferred communication protocol across diverse sectors. From automotive systems to industrial automation and even home appliances, the CAN bus’s ability to adapt and grow with evolving requirements is a testament to its robust design. Let’s delve into the aspects that contribute to the CAN bus’s flexibility and scalability.
Modular Design
The CAN bus operates on a modular design principle. This means that devices or nodes can be added or removed without needing to shut down the entire system or reconfigure the network. This plug-and-play nature ensures that systems can be easily expanded or modified as requirements change.
Multi-master Configuration
The CAN bus supports a multi-master configuration, where any node can initiate communication. This eliminates the need for a central master controller, allowing for decentralized control and reducing single points of failure. This design ensures that if one node fails, the rest of the network can continue to operate.
Standard and Extended Identifiers
The CAN protocol supports both standard (11-bit) and extended (29-bit) message identifiers. This dual system allows for a vast number of unique message IDs, ensuring that large and complex networks can be accommodated without identifier conflicts.
Data Length Flexibility
CAN messages can carry payloads ranging from 0 to 8 bytes, allowing for flexibility in the type and amount of data transmitted. This ensures that both short control commands and longer data packets can be efficiently transmitted over the same network.
Network Topology Options
While the CAN bus typically operates in a bus topology, it can also support star or hybrid topologies with the right hardware. This flexibility allows the CAN bus to be tailored to specific application requirements, whether it’s a simple linear bus in a car or a more complex network in an industrial setting.
Compatibility with Higher Layer Protocols
The CAN bus serves as the foundational layer for several higher-level protocols, such as CANopen, DeviceNet, and SAE J1939. These protocols define additional communication and application layers, allowing the CAN bus to be adapted for specific industries and applications.
Speed and Distance Scalability
The CAN bus offers a trade-off between speed and network length. High-speed CAN networks can transmit data at rates up to 1 Mbps but are limited in length. In contrast, low-speed networks can span longer distances but at reduced data rates. This flexibility ensures that the CAN bus can be optimized for both compact, high-speed systems and expansive, slower networks.
The flexibility and scalability of the CAN bus are among its most defining features. Its ability to adapt to diverse requirements, from compact automotive systems to expansive industrial networks, underscores its versatility. As technology continues to evolve and systems become more interconnected, the CAN bus’s inherent adaptability ensures that it remains a cornerstone in the world of communication protocols. Whether it’s integrating new devices, expanding network coverage, or adapting to new data requirements, the CAN bus stands ready to meet the challenges of the future.
Cost-Effective
The CAN (Controller Area Network) bus, while celebrated for its reliability, real-time capabilities, and flexibility, is also recognized for its cost-effectiveness. This economic advantage has been a significant factor in its widespread adoption across various industries, from automotive to industrial automation and beyond. Let’s explore the elements that contribute to the CAN bus’s cost-effectiveness.
Reduced Wiring
One of the most immediate cost benefits of the CAN bus is the reduction in wiring. Traditional point-to-point wiring systems require individual connections between each device or component, leading to a complex web of wires. In contrast, the CAN bus uses a single twisted-pair cable that all devices connect to, significantly reducing the amount of wiring needed.
- Material Savings: Fewer wires mean less copper and insulation material, leading to direct cost savings.
- Weight Reduction: Especially crucial in automotive and aerospace applications, reduced wiring translates to weight savings, which can improve fuel efficiency.
- Simplified Troubleshooting: A streamlined wiring system simplifies diagnostics and maintenance, reducing labor costs.
Modular Design
The modular nature of the CAN bus allows for easy system expansions or modifications without the need for extensive reconfigurations. This adaptability means that as requirements change or new technologies emerge, systems can be updated without incurring significant costs.
Standardization
The CAN protocol is standardized, ensuring that components from different manufacturers can interoperate seamlessly. This standardization:
- Promotes Competition: With multiple manufacturers producing CAN-compliant components, there’s competitive pricing, leading to cost savings for end-users.
- Avoids Vendor Lock-in: Users aren’t tied to a single manufacturer and can choose components based on cost, performance, or other criteria.
Longevity and Durability
The robust design of the CAN bus ensures longevity and durability, even in harsh environments. This reliability translates to:
- Reduced Maintenance: Fewer breakdowns and failures mean less frequent maintenance, leading to cost savings.
- Extended Lifespan: Systems that last longer reduce the need for replacements or overhauls, offering long-term cost benefits.
Scalability
The CAN bus’s scalability ensures that it can cater to both small, simple networks and large, complex systems. This scalability means that users don’t incur unnecessary costs for features or capacities they don’t need.
Reduced Training Costs
Given the widespread adoption of the CAN bus, there’s a wealth of knowledge, training resources, and tools available. This abundance reduces the training costs for technicians and engineers.
Energy Efficiency
In applications where the CAN bus aids in optimizing operations, such as in automotive or industrial settings, there can be energy savings. Efficient operations translate to reduced energy consumption, leading to cost savings, especially in sectors where energy costs are significant.
The cost-effectiveness of the CAN bus is a culmination of its design principles, standardization, and adaptability. By reducing material costs, simplifying maintenance, and ensuring longevity, the CAN bus offers tangible economic benefits. As industries continue to seek solutions that are both technologically advanced and economically viable, the CAN bus stands out as a communication protocol that strikes the right balance between performance and cost.
Error Handling
The CAN (Controller Area Network) bus is renowned for its robustness, especially in electrically noisy environments. A significant contributor to this robustness is the protocol’s comprehensive error handling mechanisms. These mechanisms ensure that data integrity is maintained, and communication disruptions are minimized. Let’s delve into the intricacies of error handling in the CAN bus.
Types of Errors
The CAN protocol classifies errors into different categories based on their nature:
- Bit Errors: Occur when a transmitting node detects a discrepancy between the transmitted bit and the bit monitored on the bus.
- Stuff Errors: The CAN bus uses bit stuffing to ensure synchronization. A stuff error is detected if the predefined bit-stuffing rule is violated.
- CRC Errors: A mismatch between the calculated CRC (Cyclic Redundancy Check) value and the received CRC value indicates a CRC error.
- Form Errors: Detected when a fixed-form field of the frame contains an illegal value.
- Acknowledgment Errors: Occur when a transmitting node doesn’t receive an acknowledgment for its transmitted message.
Error Detection Mechanisms
The CAN bus incorporates several mechanisms to detect and handle errors:
- Monitoring: Every node that transmits a message also monitors the bus to verify that the transmitted message matches the bus activity. Discrepancies indicate errors.
- Cyclic Redundancy Check (CRC): Each CAN message includes a CRC sequence. Receivers calculate the CRC for the received message and compare it to the transmitted CRC. Mismatches indicate errors.
- Bit Stuffing: To ensure synchronization, the CAN protocol introduces additional bits (called stuff bits) after a sequence of bits with the same value. If receivers detect a violation of this rule, they flag a stuff error.
Error Signaling
When a node detects an error, it signals the error by transmitting an “error flag,” which consists of six consecutive dominant bits. This error flag:
- Alerts other nodes: All other nodes detect the error flag and know that an error has occurred.
- Initiates error confinement: Nodes that detect their own transmission errors classify them as “transmit errors” while nodes that detect errors during message reception classify them as “receive errors.”
Error Confinement
The CAN protocol is designed to identify and isolate faulty nodes to prevent them from disrupting the entire network:
- Error Counters: Each node maintains two error counters – one for transmit errors and one for receive errors. When a node detects an error, the relevant counter is incremented.
- Error Passive Mode: If either of a node’s error counters exceeds a certain threshold (typically 127), the node enters an “error passive” state. In this state, the node still participates in bus activities but becomes more cautious in its transmissions.
- Bus Off Mode: If a node’s transmit error counter exceeds a higher threshold (typically 255), the node enters the “bus off” state. In this state, the node is effectively disconnected from the bus and must undergo a recovery process before resuming communication.
Error Recovery
Nodes in the “bus off” state can’t initiate new communications but can listen to bus activities. To rejoin the network:
- Automatic Recovery: Some systems are configured to allow nodes to automatically rejoin the network after a predefined time or after observing a specific number of clean (error-free) messages on the bus.
- Manual Recovery: In other systems, manual intervention might be required to reset and reintegrate a node into the network.
The comprehensive error handling mechanisms of the CAN bus underscore its reliability and robustness. By swiftly detecting, signaling, and confining errors, the CAN protocol ensures that communication remains consistent and trustworthy, even in challenging environments. This robust error handling, combined with other features like real-time capabilities and flexibility, solidifies the CAN bus’s position as a premier communication protocol in various industries.
-Limitations
Bandwidth Limitations
The CAN (Controller Area Network) bus, while celebrated for its robustness, real-time capabilities, and error handling, does have inherent bandwidth limitations. Understanding these limitations is crucial when designing systems, especially in applications that require high data throughput or operate in large networks. Let’s delve into the bandwidth constraints of the CAN bus and their implications.
Definition of Bandwidth in CAN
Bandwidth, in the context of the CAN bus, refers to the maximum rate at which data can be transmitted over the network. It’s typically measured in bits per second (bps) or Megabits per second (Mbps). The bandwidth of a CAN bus is influenced by several factors:
- Bit Rate: The speed at which bits are transmitted on the bus. Higher bit rates allow for faster data transmission but can limit the maximum length of the network.
- Message Length: CAN messages can vary in length, with longer messages taking more time to transmit.
- Bus Load: The percentage of time the bus is actively transmitting data. A higher bus load can lead to congestion and reduced effective bandwidth.
Inherent Limitations
- Standard Bandwidth Caps: The classic CAN (CAN 2.0A and CAN 2.0B) supports maximum bit rates up to 1 Mbps. While this is sufficient for many applications, it may not meet the needs of systems that require high data throughput.
- Network Length vs. Bit Rate Trade-off: As the bit rate increases, the maximum allowable length of the CAN bus decreases. For instance, at 1 Mbps, the network length might be limited to 40 meters, while at 125 kbps, it could extend up to 500 meters. This trade-off can be a limitation in expansive systems.
- Overhead: The CAN protocol includes various fields for error checking, arbitration, and signaling. This overhead can reduce the effective bandwidth available for actual data transmission.
Implications of Bandwidth Limitations
- Data Latency: In networks with high bus loads or where large amounts of data need to be transmitted, bandwidth limitations can introduce latency. This can be problematic in real-time applications where timely data transmission is crucial.
- Network Design Constraints: Systems that require high bandwidth might need to be segmented into multiple CAN networks or might necessitate the use of alternative communication protocols.
- Potential for Bus Congestion: In scenarios where multiple nodes attempt to transmit data simultaneously, bandwidth constraints can lead to bus congestion, increasing the likelihood of message collisions and delays.
Overcoming Bandwidth Limitations
- CAN FD (Flexible Data Rate): CAN FD is an extension of the classic CAN protocol, allowing for bit rates beyond 1 Mbps and larger data payloads. This effectively increases the available bandwidth for data transmission.
- Network Segmentation: Dividing a large CAN network into smaller sub-networks, interconnected through gateways or bridges, can help manage bandwidth limitations.
- Hybrid Systems: In systems with varied bandwidth requirements, a hybrid approach can be adopted, where the CAN bus handles real-time, low-bandwidth communications, and other protocols (like Ethernet) manage high-throughput data.
While the CAN bus offers numerous advantages, it’s essential to be cognizant of its bandwidth limitations, especially when designing systems for high-throughput applications. By understanding these constraints and leveraging solutions like CAN FD or hybrid systems, designers can harness the strengths of the CAN bus while effectively managing its limitations. As technology continues to evolve and data requirements grow, the continuous adaptation and integration of communication protocols will be key to meeting these challenges.
Network Length Restrictions
The CAN (Controller Area Network) bus is a differential communication system, renowned for its robustness and reliability. However, like all communication systems, it has inherent limitations, one of which is the restriction on the maximum length of the network. This limitation is influenced by several factors and has implications for system design and performance. Let’s delve deeper into the network length restrictions of the CAN bus.
Factors Influencing Network Length
- Bit Rate: There’s an inverse relationship between the bit rate (speed of data transmission) and the maximum allowable network length. Higher bit rates allow for faster data transmission but reduce the maximum length of the CAN bus. Conversely, lower bit rates permit longer network lengths but at the cost of reduced data transmission speed.
- Propagation Delay: This is the time taken for a signal to travel from one end of the network to the other. As the network length increases, so does the propagation delay. If this delay becomes too significant, it can interfere with the timely detection and acknowledgment of messages, leading to communication errors.
- Signal Attenuation: As the signal travels longer distances, it tends to weaken or attenuate. If the signal attenuates too much, it might not be detectable or distinguishable at the receiving end.
- Electromagnetic Interference (EMI): Longer cables can act as antennas, picking up more electromagnetic interference. This can introduce noise into the system, affecting data integrity.
Typical Network Lengths Based on Bit Rate
- 1 Mbps: Up to 40 meters
- 500 kbps: Up to 100 meters
- 250 kbps: Up to 250 meters
- 125 kbps: Up to 500 meters
- 50 kbps: Up to 1 kilometer
(Note: These are general guidelines, and actual lengths can vary based on factors like cable quality, network topology, and environmental conditions.)
Implications of Network Length Restrictions
- System Design: Designers need to be cognizant of the network length restrictions, especially when setting up expansive systems like industrial automation networks or public transportation systems.
- Performance Trade-offs: There’s a trade-off between speed and distance. Systems requiring high-speed data transmission might be constrained in terms of maximum network length, while those that can tolerate slower data rates can be more expansive.
- Segmentation and Repeaters: For very large systems, the network might need to be segmented into smaller sub-networks. Repeaters can be used to amplify and retransmit signals, effectively extending the network’s range.
- Choice of Cable: The quality and type of cable used can influence the maximum network length. High-quality, shielded cables can reduce signal attenuation and interference, potentially allowing for longer network lengths.
Overcoming Network Length Restrictions
- Use of Repeaters: Repeaters can receive, amplify, and retransmit signals, effectively extending the range of the CAN network.
- Hybrid Systems: In expansive systems, the CAN bus can be combined with other communication protocols that support longer distances, with gateways facilitating communication between different segments.
- Optimized Network Topology: Using star or hybrid topologies, where feasible, can help manage length restrictions more effectively than a pure bus topology.
While the CAN bus offers numerous advantages, understanding its network length restrictions is crucial for effective system design. By being aware of these limitations and leveraging solutions like repeaters, hybrid systems, and optimized topologies, designers can create efficient and reliable CAN-based communication systems that meet the specific needs of their applications. As technology continues to advance, finding innovative ways to manage and extend the capabilities of the CAN bus will remain a focal point in the realm of network design.
Security Concerns
The CAN (Controller Area Network) bus, initially designed for automotive applications, prioritized reliability, real-time communication, and error handling. However, as the interconnectedness of devices has grown and the CAN bus has found applications beyond vehicles, security concerns have become increasingly prominent. Let’s delve into the security vulnerabilities of the CAN bus and the implications of these concerns.
Inherent Vulnerabilities
- Lack of Authentication: The standard CAN protocol does not have built-in mechanisms for authenticating messages or nodes. This means any node on the network can transmit messages, making it susceptible to spoofing attacks where malicious nodes impersonate legitimate ones.
- No Encryption: CAN messages are transmitted in plaintext without encryption. This lack of encryption makes it easy for attackers with access to the network to eavesdrop, intercept, and understand the data being communicated.
- Replay Attacks: Without mechanisms to ensure the freshness of messages, attackers can capture legitimate messages and replay them at a later time, potentially causing unintended actions.
- Denial of Service (DoS) Attacks: Malicious nodes can flood the network with high-priority messages, preventing legitimate messages from being transmitted and effectively causing a denial of service.
Implications of Security Vulnerabilities
- Vehicle Safety: In automotive applications, a compromised CAN bus can affect critical systems like brakes, airbags, and engine controls. This can pose significant safety risks to passengers and other road users.
- Industrial Sabotage: In industrial settings, a malicious actor could disrupt machinery, halt production lines, or even cause physical damage by sending unauthorized commands over the CAN network.
- Data Theft: In applications where sensitive data is transmitted over the CAN bus, eavesdropping can lead to data theft, with potential implications for privacy or intellectual property.
- Loss of Trust: Security breaches can erode trust in connected systems, potentially slowing the adoption of new technologies or leading to financial and reputational damages for manufacturers.
Addressing Security Concerns
- Higher Layer Protocols: Some higher-layer protocols built on top of the CAN bus, like CANopen and SAE J1939, introduce security features, although they might still not offer comprehensive protection.
- Hardware-based Security: Secure hardware modules can be integrated into CAN nodes to provide encryption, authentication, and other security features.
- Message Authentication Codes (MACs): By adding MACs to CAN messages, nodes can verify the authenticity and integrity of received messages.
- Intrusion Detection Systems (IDS): IDS can monitor network traffic for anomalies or known attack patterns, alerting system administrators to potential security breaches.
- Firewalls: Hardware or software-based firewalls can be used to filter incoming and outgoing CAN messages, ensuring only legitimate messages are transmitted.
- Regular Updates: Keeping firmware and software updated can help address known vulnerabilities and improve the overall security posture of CAN-based systems.
While the CAN bus offers numerous advantages in terms of reliability and real-time communication, its security vulnerabilities cannot be overlooked, especially in today’s interconnected world. As the applications of the CAN bus expand and the potential consequences of security breaches become more severe, addressing these concerns becomes paramount. Through a combination of hardware solutions, software enhancements, and best practices, it’s possible to bolster the security of the CAN bus, ensuring it remains a trusted communication protocol for various applications.
Complexity in Large Networks
The CAN (Controller Area Network) bus, initially designed for automotive systems with a limited number of nodes, has seen widespread adoption in various industries, from industrial automation to aerospace. As the scale of these networks grows, so does their complexity. Managing this complexity is crucial for ensuring reliable communication, timely data transmission, and overall system efficiency. Let’s explore the challenges and implications of complexity in large CAN bus networks.
Challenges in Large Networks
- Increased Traffic: As the number of nodes in a CAN network increases, so does the volume of messages being transmitted. This can lead to bus congestion, increased latency, and potential message collisions.
- Arbitration Delays: The CAN bus uses a priority-based arbitration mechanism to resolve message collisions. In large networks with many nodes transmitting simultaneously, arbitration can introduce delays, affecting real-time communication.
- Network Topology: While the CAN bus typically uses a linear bus topology, large networks might require more complex topologies, like star or hybrid configurations. Managing these topologies can introduce challenges in signal integrity, synchronization, and network design.
- Error Propagation: In expansive networks, an error in one segment or node can propagate and affect other parts of the network, leading to widespread communication disruptions.
- Diagnostics and Troubleshooting: Identifying and rectifying faults in large networks can be time-consuming. Pinpointing a malfunctioning node or segment becomes more challenging as the network grows.
- Power Management: Extensive networks, especially those spanning large physical areas, can face challenges in ensuring consistent power delivery to all nodes.
- Security Concerns: Larger networks, by virtue of their scale, can have more potential entry points for malicious actors, increasing the risk of security breaches.
Managing Complexity
- Segmentation: Dividing a large CAN network into smaller sub-networks or segments can help manage traffic and reduce congestion. Gateways or bridges can be used to facilitate communication between these segments.
- Advanced Diagnostics Tools: Utilizing advanced diagnostic tools and software can aid in real-time monitoring, fault detection, and troubleshooting in expansive networks.
- Redundancy: Implementing redundant paths or nodes can enhance reliability. If one path or node fails, the redundant component can take over, ensuring uninterrupted communication.
- Optimized Network Design: Careful planning and design, considering factors like node placement, cable quality, and topology, can mitigate challenges associated with large networks.
- Higher Layer Protocols: Protocols like CANopen or SAE J1939, built on top of the basic CAN protocol, offer features tailored for larger networks, including advanced communication modes, network management functions, and standardized profiles.
- Security Measures: Implementing firewalls, intrusion detection systems, and secure hardware modules can enhance the security of large CAN networks.
The complexity of large CAN bus networks, while challenging, is not insurmountable. With careful planning, the use of advanced tools and protocols, and a focus on best practices, it’s possible to manage this complexity effectively. As the demand for interconnected devices and systems continues to grow, understanding and addressing the challenges of large CAN networks will be crucial for ensuring reliable, efficient, and secure communication.
The CAN bus, with its myriad advantages, has revolutionized communication in various sectors. Its reliability, real-time capabilities, and flexibility make it a preferred choice for many applications. However, understanding its limitations is crucial to ensure that it’s used in scenarios where it can offer the most value. As technology continues to evolve, it’s likely that the CAN bus will adapt, further cementing its importance in the world of communication protocols.
Frequently Asked Questions
Final Thoughts
The CAN bus system has revolutionized the way devices communicate in a network, especially in the automotive industry. Its robustness, flexibility, and cost-effectiveness make it a preferred choice for many industries. The most important takeaway from this article is the understanding of the significance of the CAN bus system in modern electronics and its potential for future applications. As industries continue to evolve, the CAN bus will undoubtedly play a pivotal role in the development of interconnected systems.
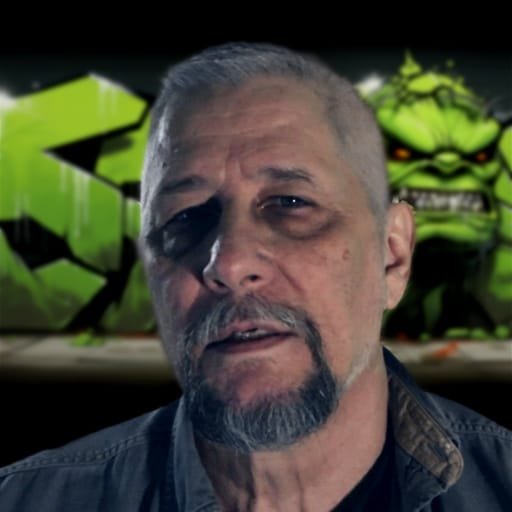
I write for and assist as the editor-in-chief for 601MEDIA Solutions. I’m a digital entrepreneur since 1992. Articles may include AI assisted research. Always Keep Learning! Notice: All content is published for educational and entertainment purposes only. NOT LIFE, HEALTH, SURVIVAL, FINANCIAL, BUSINESS, LEGAL OR ANY OTHER ADVICE. Learn more about Mark Mayo